Introduction
Due to their complexity, many processes cannot be automated or not completely automated by conventional technical solutions, because the operational control of these processes requires the know-how of experts (often gathered over years). This is also the case with the breeding of shrimps. Determining the number and size of shrimps is crucial for good system control, for example of feed supply, yield and the economic performance of the farm. If, for example, too much feed is added, water quality deteriorates and if too little feed is added, growth is inhibited. To determine the biomass, manual samples are taken regularly, and an estimate is made based on these samples. To optimize the control and minimize the manual effort, continuous data acquisition and evaluation will be realized in this project by methods of Computer Vision, Machine Learning and Internet of Things.
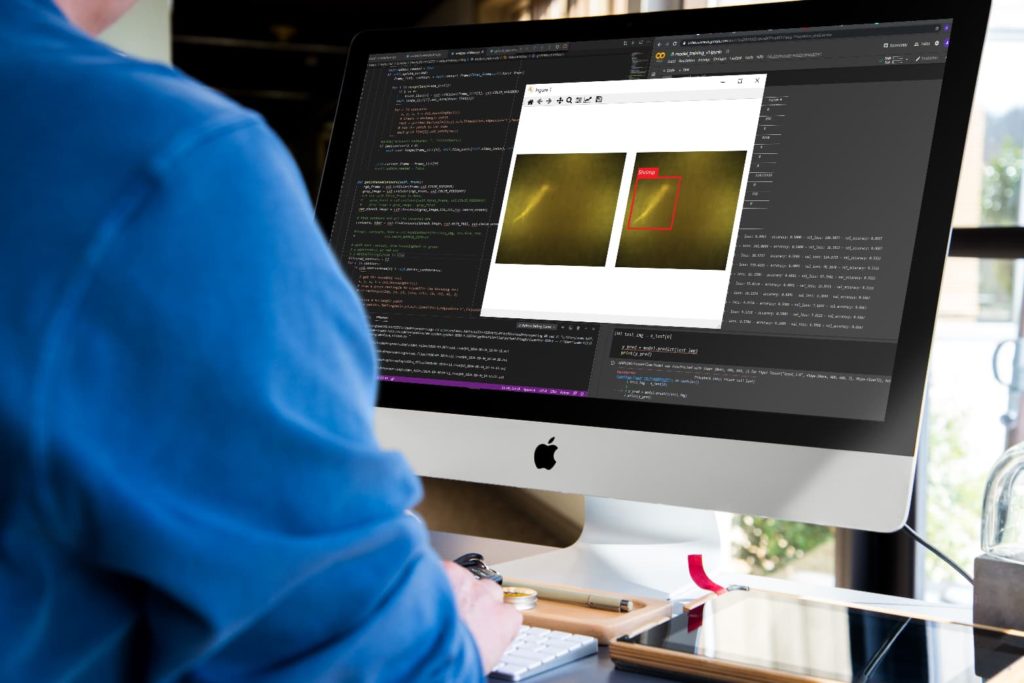
Procedure
The integration of the different components and the structure of the designed concept is shown in the figure below.
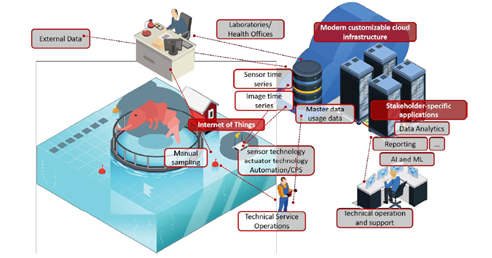
The procedure can be divided into three main topics:
- Preprocessing (local, or „on the edge“)
A local computer uses an underwater camera to record and filter data in a pool. Shrimp detection is performed, which is implemented with machine learning methods. If a shrimp is detected in the recording area, this sequence is saved as a video file and uploaded to the cloud. - Analysis of the pre-processed data (globally, or “in the cloud”)
The filtered data is then further processed in the cloud. The image data is used, for example, to estimate the size of individual shrimps to be able to track the growth process. - Adaption of the control system
Based on the generated and already existing data the control system of the shrimp farm is optimized. All existing data from laboratory results to technical specifications will be integrated.
Profit
The designed concept combines computer vision with concepts of the Internet of Things. This combination makes it possible to generate new input parameters for a control system in different application areas. A possible loss of information and the use of unsystematic reference values are reduced, thus enabling the automation of these processes. This means that the manual effort for control by in-situ measurements can be reduced significantly or even completely. At the same time, it is possible to compare data, control parameters and the performance of different locations, to identify best practices and to exchange them across locations.
This project was carried out as part of the European project Digital Innovation Hubs for Cyber-Physical Systems (DIH4CPS). The grand number is 872548.