CPS for optimized production of customized machinery tools
This Project Initial Application Experiment will increase capacity utilization and optimize production based on custom orders for SMEs.
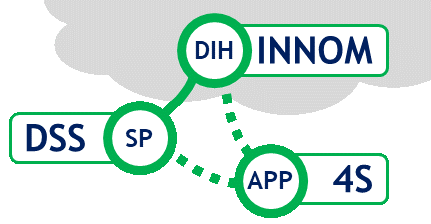
4S 2000 is a machinery company in a disadvantaged Nuts2 region (among the ten less developed region within the EU). Production planning is currently not supported with digital tools at all, it is based on estimates and the routines of production managers (therefore errors can occur, no use of historical data, etc). As a result, the utilization of available capacity is not optimal, the time to complete orders may be delayed. Ultimately the lower capacity utilization and efficiency losses result in higher cost of production (decreased competitiveness of the company).
Solution: Develop and implement a capacity planning and production optimization solution. At the moment the company uses CNC machines with Embedded Systems. This traditional solution will be enhanced by implementing the use of sensors thus obtaining data about the production process. By feeding and analyzing this data by a cloud-based online solution a CPS is created.
The capacity planning tool will compare the production plans towards the facts in the factory (prepared and in progress orders in delivery phase). The manufacturing planning and optimization software will be able to create the optimal production schedule for dynamically changing orders with its modeling and optimizing function.
Partner | Expertise | Role |
---|---|---|
Innomine DIH | Innomine is a digital innovation hub, focusing on digital transformation, smart manufacturing, Industry40 and related fields (in HPC, cloud, AI, Blockchain and other technologies). | DIH |
4S-2000 Ltd | 4S-2000 Ltd. is a company specializing in industrial machinery, located in one of the less developed Nuts2 regions of EU. The primary activities of the company include the production of machinery and parts, metalworking, as well as designing and producing manufacturing equipment. | Technical Partner |
DSS | DSS Consulting Ltd. – located in Budapest, Hungary – has been specializing on Business Intelligence systems, implementing analytical solutions and customized applications. | ISV |
Problem/Business Case description
The planned execution and identification system for SMEs will automatically provide information about production planning. It will integrate appropriate sensors recording the number of operations, and different steps of the operation . A tablet module will allow the workers to enter the start and end of the operation for the job number giving real-time information about the operation of the actual production processes. This provides additional analysis, fine tuning and optimization options.
Within the planned experiment, it will be possible to allocate costs for each resource and its lifetime: the overhead cost of the machine over time and the cost of a variable for a given operation, the cost of labor per unit time, overhead and operational and other costs. This will allow carrying out design and optimization steps and minimize costs. This provides further business optimization opportunities for the end-user (4S 2000) and will support the company to make informed decisions on production orders with tight deadlines.
AE description
At the end-user (manufacturing company) the basic steps of digitization have already taken place, and we will use these results (primarily available data) to develop and optimize the operation of the whole plant. Using the capacity planning and manufacturing optimization solution, the existing narrow production cross-sections (machine and man) will be revealed. By expanding or modifying these, further optimization steps can be taken by the factory management to synchronize dynamically changing order stock and capacity / production. Optimized capacity and production planning will allow to reduce warehouse inventory levels and production lead times.

By analyzing the capacity utilization data, the production plans, the data of the operations performed by the individual employees and the other production data used in the system, the factory management will gain further insight into the development. This system will also serve as a manufacturing assistant, appearing at each production point, which will represent a major cultural change in the manufacturing process of SMEs, the entry of workers into a new digital world, and the preparation of further automation and robotization steps.
The system will be cloud-based, will integrate data of machines and sensors and an easy-to-scale IT solution that can be easily implemented for manufacturing SMEs.